Scientists from PNIPU have developed a new method for creating metal blanks using layer-by-layer plasma metallization. This method, which is still largely unexplored, produces high-quality, defect-free parts such as crankshafts and bearing housings. Unlike traditional melting technologies, it can significantly increase productivity and improve the performance of finished products.
Additive technologies allow you to create parts with different shapes and properties by applying material layer by layer according to a digital model. Traditional methods use melting of the starting material, which often results in defects due to overheating and temperature instability. The new method uses additive technology combined with cold gas dynamic spraying followed by laser and plasma remelting, which helps to avoid such problems and produce parts with minimal defects.
Plasma metallization allows one or more wires to be used to create blanks, which makes it possible to precisely control the composition and properties of the material. In the experiments of scientists from PNIPU, heat- and corrosion-resistant steel was used. Tests have shown that the new blanks have excellent mechanical properties and can be used in various branches of mechanical engineering. This technology promises to revolutionize the production of metal parts, increasing their quality and productivity.
Source: Ferra
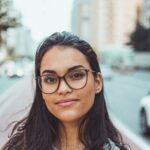
I am a professional journalist and content creator with extensive experience writing for news websites. I currently work as an author at Gadget Onus, where I specialize in covering hot news topics. My written pieces have been published on some of the biggest media outlets around the world, including The Guardian and BBC News.