Typically, the production of individual prostheses lasts for several weeks, but the new system allows you to reduce this period to several days. First, a digital joint model is created based on the patient’s CT or MRI diagnoses. Then, a plastic prototype is printed on a 3D printer used to control the functionality and prepare for the process.
The latest version of the device made of titanium is then sent to production. The development said that doctors allow doctors to evaluate all the nuances of the operation and to adjust the prostheses correctly to the patient’s anatomical characteristics.
According to experts, it simplifies the process of combining all stages into a single digital chain and makes personalized prostheses available not only in large clinics, but also in ordinary medical institutions. This can significantly expand the possibilities of the treatment of patients in need of individual implants.
Source: Ferra
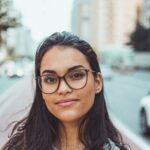
I am a professional journalist and content creator with extensive experience writing for news websites. I currently work as an author at Gadget Onus, where I specialize in covering hot news topics. My written pieces have been published on some of the biggest media outlets around the world, including The Guardian and BBC News.