Since its launch, Tesla has had an extremely ambitious plan: to produce the best electric cars while optimizing its processes as much as possible. The manufacturer has already innovated a lot in this section since the launch of its gigafactories, which have since significantly increased production volumes.
However, with the increase in demand that Tesla has experienced in recent years, the company needs to further optimize its processes. Not only to reduce costs, but also to provide greater flexibility by simplifying production.
In fact, it is planned to implement a new casting process that could significantly reduce costs and simplify vehicle production beyond the capabilities of the rest of the industry, which would undoubtedly mean a competitive advantage over other manufacturers, even those that have been in the industry for more than half a century.
According to sources ReutersThe new process will allow the automaker to cast almost the entire lower section of the car as a single unit. This is a very ambitious step, since today it is necessary, depending on the model and manufacturer, to manufacture and weld about 400 parts using traditional technologies used in the industry.
A process that started with the Tesla Model Y
It’s a process similar to what Tesla uses on the Model Y, some parts of which are made using a proprietary ultra-high-pressure compression molding process that molds both the front and rear of the car. New process will allow the use of similar technology, with some nuancesfor the entire lower half of its cars, not limited to just the Model Y. Once this new process is up and running, Tesla will be able to produce the entire lower half of its cars.
Keep in mind that there is a reason why manufacturers use multiple parts to make bass guitars. Usually the underbody is made by welding the parts, leaving the subframe open, which is completely hollow and constructively assists the vehicle in the event of an accident.
However, Tesla also has a solution to preserve the hollow subframe structure: a new shape incorporating 3D printed hard sand cores. After printing and casting the product, the sand is removed. leaving the same hollow structure without the need to weld the parts together.
It is unknown when Tesla will be ready for the new process, but it could certainly be a huge change that will revolutionize the electric vehicle industry and also take advantage of the innovation that this type of vehicle allows in terms of production due to the reduction in the number of moving parts before him – to normal.
Source: Hiper Textual
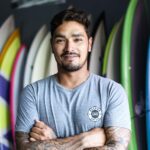
I’m Blaine Morgan, an experienced journalist and writer with over 8 years of experience in the tech industry. My expertise lies in writing about technology news and trends, covering everything from cutting-edge gadgets to emerging software developments. I’ve written for several leading publications including Gadget Onus where I am an author.