Vibranium, a super-strong material typical of the Marvel Universe, does not exist in real life. But the truth is that Captain America will have no shortage of materials to create his shield. Actually new super durable materialrecently developed by scientists from RMIT Universityfrom Australia would be an ideal candidate.
This titanium alloy, 3D printing, with a structure inspired by nature. The result is a material that is 50% stronger than the next strongest alloy of similar density. This is a magnesium alloy called WE54but he is far behind.
And, in addition to the special design inspired by nature, the creators of this ultra-durable material used an unconventional, but very effective and inexpensive printing technique. The result is perfect, but they want to go further and solve some small problems that would give it endless properties in such diverse areas as medicine or space industry.
How was this ultra-strong material created?
It’s actually a metamaterial. This concept is somewhat vague. There is no precise definition, but it is generally used to refer to man-made materials that have different electromagnetic characteristics to the components of its components, in this case titanium.
Its structure is based on the structure of certain natural structures, which, although thin and flexible, are at the same time hard and resistant. This is the case, for example, with the stem Water lily Victoria or corals of the species Tubipora music. But there is a problem.
When attempts were made to create materials that imitated their structure, this proved impossible. distribute the load equally. That is, if force is applied to them, some points will be subject to greater stress, which can lead to destruction.
However, this problem has been solved thanks to the new design and the advantages that 3D printing brings. One of those responsible for the investigation explained this in a statement: Ma Qian.
“We developed a hollow tubular lattice structure with a thin strip running inside it. Together, these two elements demonstrate strength and lightness never before seen together in nature. By effectively combining two complementary lattice structures to distribute stress evenly, we avoid weak points where stress typically concentrates.”
Ma Qian, author of the study.
For printing methodused a printer that melts layers of metal powder using high power laser. The result, as expected, is a super-strong material in which stress is distributed evenly throughout its structure.
So what now?
The authors of the study, published in Advanced Materials, want to further improve this ultra-durable material. In particular, they hope to make improvements that will also make it more resistant to heat. It can already withstand temperatures of 350°C, but it is believed that with some modifications it can reach temperatures of 350°C. withstand 600°C.
In this case, since it is a scalable material that can be used in different sizes, it can be used for e.g. rockets or drones for firefighters. There’s just one problem. Printers that use lasers to melt metal powder are unusual. Therefore, quickly bringing this material to industrial scale will not be easy.
All will pass. He’s currently in the research stage and everything he can do will appeal to the best of superheroes.
Source: Hiper Textual
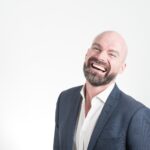