The Russian aviation industry is actively working to increase the production of domestic gas turbine engines, which are not inferior to world standards in terms of quality. One of the most complex parts of such engines are gas turbine blades, which are exposed to very high temperatures and pressures. To cool these blades, many small holes are drilled in them, which is quite difficult due to their shape. Scientists from the Perm Polytechnic have created a new program that improves the quality and accuracy of these holes. This allows modern CNC machines to work faster and more efficiently, reducing the risk of damage.
High-pressure turbine blades are subjected to heavy loads and are cast from heat-resistant nickel alloys. To cool them, small holes of only 0.5-0.8 millimeters in diameter are used, through which compressed air is supplied. Due to the high stress on the edges of the holes, they can quickly fail, so their edges are rounded to reduce stress and prevent failure.
Now rounding is carried out on machines using the electric discharge milling method, in which an electrode drills holes using electric discharges. But for better cooling, the holes must have a complex shape, which complicates the task of precise placement. Scientists of the Perm Polytechnic have developed a mathematical model and algorithm that allow you to accurately calculate the coordinates and shape of the rounding. This significantly increases the accuracy of processing, which was confirmed by tests of the new program. It can be implemented at domestic enterprises to improve the production of gas turbine engines.
Source: Ferra
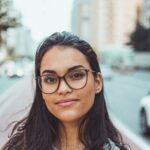
I am a professional journalist and content creator with extensive experience writing for news websites. I currently work as an author at Gadget Onus, where I specialize in covering hot news topics. My written pieces have been published on some of the biggest media outlets around the world, including The Guardian and BBC News.