Researchers from Tomsk Polytechnic University studied how the fuel droplets break down and determined the optimal parameters for their combustion. The scientists’ work was published in the journal Fuel.
If the operating parameters of fuel-oil engines are incorrect – with an excess or lack of air – the latter, as a rule, does not have time to burn out and reaches the walls of the equipment. The resulting soot deposits can cause the wall to overheat. Studies have shown that a 2% increase in fuel combustion efficiency will save more than $1.5 billion per year.
There are two types of fuel oil atomization – primary grinding in the pneumatic nozzle device and secondary, where the fuel droplets collide with the walls of the equipment or solid particles in an aerosol stream. The researchers studied the second case – with this you can achieve the minimum droplet size with minimal energy cost.
During their experiments, they pushed the fuel through a solid substrate and looked at how it was affected by the temperature of the fuel and the walls of the equipment, the water concentration in the composition, the size of the droplets and their velocity. spraying. Scientists have found that the optimum temperature of the water-oil emulsion is 80 °C, and the wall temperature is more than 200 °C. With such parameters, less soot is formed and the drops are “crushed” more efficiently, which reduces ignition times and increases the completeness of combustion. In this case, the water concentration should be about 10%.
Source: Ferra
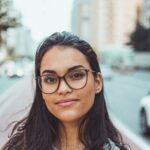
I am a professional journalist and content creator with extensive experience writing for news websites. I currently work as an author at Gadget Onus, where I specialize in covering hot news topics. My written pieces have been published on some of the biggest media outlets around the world, including The Guardian and BBC News.