Experts from Perm National Research Polytechnic University have developed and patented a new method for automatic calibration of a 3D printer.
Scientists say their current methods are flawed. Its main disadvantage is that the nozzle through which the printing material is supplied is pressed onto the 3D printer table. Therefore, the platform may collapse and the products may be deformed. Also, in almost all methods, distance sensors can only measure a limited number of points from the nozzle to the table, indicating a poor setting quality.
The researchers placed a microservo on top of the printer. It serves to move the lower part from horizontal to vertical position by means of a hinge-like swivel.
Based on the data received by the distance sensors, the control unit calculates the required degree of pressing on the table. The lower part of the calibration mechanism is lowered to the desired level and with a signal from the control unit, the servo drives act on the spring mechanisms that correct the height of the platform by producing a predetermined number of revolutions.
After the required accuracy is set, the microservo driver returns the bottom of the mechanism to its original position.
Source: Ferra
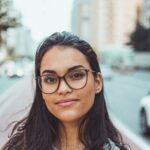
I am a professional journalist and content creator with extensive experience writing for news websites. I currently work as an author at Gadget Onus, where I specialize in covering hot news topics. My written pieces have been published on some of the biggest media outlets around the world, including The Guardian and BBC News.